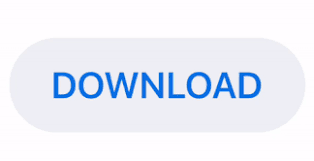
Of course, one option is to dive into your CAD system, split them and add in fixtures (think: dowels and such), but Magics does the job more efficiently.įig. While machines are getting bigger in their capacity, it’s often the case that you’ll have a couple of components that simply don’t fit. Working with large partsĪnother key issue that Magics provides tools to overcome is working with parts that exceed your build volume. The tools allow you to add thickness as well as to bring together the whole model into a single entity (rather than separate geometry sets for walls, doors, roofs etc). This centres on the fact that if you scale down a model of a housing complex, for example, that action also scales down wall thicknesses to such a degree that would be typically unprintable. It’ll allow you to split up those STLs that are output in a single lump.įor those that are building scale models, particularly those in perhaps the oil and gas industry or the architectural design world, there’s also a set of tools to assist with the effect of scaling large models. If you’re bulk loading data, it’ll allow you to work through each component at a time. No matter the problem, no matter how bad it is, the chances are that Magics will fix it - either with automated tools or allowing you to dive in and do it manually. Magics includes tools that allow you to take in STL data and fix it. Any of these can play havoc with your 3D print process. With any tessellated format and particularly with complex, organic shapes, triangles can be flipped, can intersect or just be plain missing. The problems often pertain to how they’re generated, rather than the formats themselves. The STL file format is the lingua franca of 3D printing - it’s not ideal, it’s a tricky little bugger at times, but it works. Not only does it include a huge range of data fixing and manipulation tools to ensure you get the best part geometry, but increasingly supports the build process for those with industrial level requirements in terms of multiple machines, multiple materials and a heavy throughput. Developed over the last 17 releases by Belgian wizards of all things 3D printing, Materialise, it’s become the de facto standard for those at the business end of 3D printing. This is where Magics steps into the fray.
#Materialize magics software#
And not everything can be solved with the included software or the CAD tools we use to initially create the 3D geometry in the first place. While many of these quickly become apparent when you dive into 3D printing for the first time, many will emerge with time. There are also a number of common place tasks that aren’t immediately obvious, whether it’s the need to split larger parts into chunks that fit into your machine, the need to compensate for z level contraction of parts after building or just fixing bad STL data. For those that have been actively building their own parts using the diverse range of technologies available, you’ll be aware that each machine and process type has its own requirements, limitations, tweaks and best practice. The fact is, as anyone who’s done this first hand knows, this is complete and utter nonsense. Magics’ 3D nesting application can optimise stackable build chamber layouts
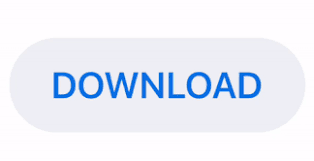